All in on insulation
Harold Orr (BE’59, MSC’63) looks back on his work designing the famed Saskatchewan Conservation House (SCH) with a mix of pride and disappointment, but still with a dash of hopefulness.
By KATHY FITZPATRICKOrr and his colleagues attained an unheard of level of energy efficiency with their findings leading to Canada’s R-2000 voluntary building standard, and the start of the passive house movement in Europe.
However, more than 40 years later, the project’s real lessons of superinsulation and airtightness have yet to be fully implemented across Canada, said Orr.
In energy savings, most housing still doesn’t come close to what could be achieved with available technology. Was this a lost opportunity for Saskatchewan?
“Yes, very much,” Orr replied.
Nevertheless, at age 88, Orr continues his work.His achievements are bringing him recognition—induction into the Order of Canada earlier this year, and a string of other national and international awards within the past decade. Will he ever stop hammering on the message of energy conservation?
“When they bury me.”
Measuring air temperature
By the time Orr got a job at the National Research Council in Saskatoon, he had already been working on an instrument to measure how fast the air was changing in buildings. It was the topic of his master’s thesis in mechanical engineering at the University of Saskatchewan (USask).
Back then, it was widely known how to calculate heat loss from insulation values.
“But when it came to how fast the air was leaking, you wet your finger and held it up to see which way the wind was blowing and then you grabbed a number out of the air and you wrote it down quickly and hoped you were within a hundred per cent of what it actually was,” Orr recalled.
At the NRC, Orr continued his work on measuring air leakage.
The Arab oil embargo of the early 1970s prompted the Saskatchewan government to commission the design and construction of a solar house suited to the climate here. Orr was asked to join the project committee.
He said he and a few other members did some “back of the envelope calculations” and concluded solar energy would take “an Olympic-size swimming pool” to hold the water needed to heat a conventional house in winter.
“And this just didn’t make sense,” he said.
They looked at reducing the heating required. At the time R7 insulation was the standard, Orr said. He suggested at least R40 for the walls, at least R60 for the ceiling, and no basement since it is one of the largest components of heat loss.
The vapour barrier was another critical element.
“It was likely the tightest house in the world at that time,” Orr said, achieving a rate of air change between 1/20 and 1/40 of the average house back then.
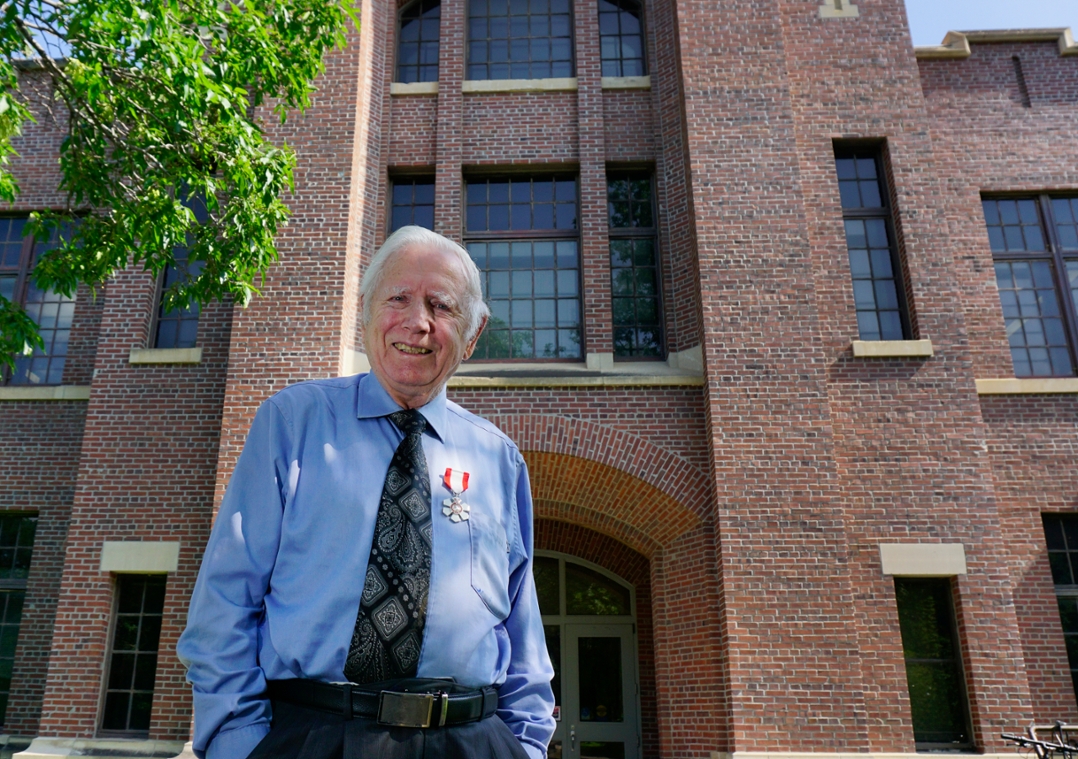
A technician at USask manufactured an air-to-air-heat exchanger to provide suitable ventilation.
The design cut the house’s energy requirement by 90 per cent, an “amazing achievement” said architect and fellow committee member Gary Marvin.
But the solar energy system roughly doubled the cost of construction—to $125,000—the pair recalled. (Back then solar technology was much costlier than it is today.)
By contrast, the team estimated it would have taken about $25 worth of natural gas per year to heat the house, Orr noted.
The SCH was sold, and later the solar system was removed because of its exorbitant maintenance cost.
But before then, people had come from around the world to view the SCH “and then it was sort of forgotten here,” said Orr’s wife Mary.
However, a visitor, Wolfgang Feist, carried the idea back to Germany, Orr said, resulting in the passive house (passivhaus) concept that "now has come back to North America."
Conservation “godfather”
Everyone associated with the passive house movement regards Orr as the “godfather of energy conservation in buildings,” Marvin said.
At the 2015 International Passive House Conference in Leipzig, Germany, Orr received the Pioneer Award for his work on the SCH.
Projects such as the passive house on Saskatoon’s Temperance Street, rare though they still are here, give Orr optimism.
And he’s still finding advances others have developed, such as technology to seal the holes in heating ducts. He said it can dramatically reduce the leakiness of a house—taking it from 17 air changes per hour to less than half an air change per hour.
“Tighter than the Saskatchewan Conservation House, in about two hours (to do the job),” Orr noted, and at a cost of $3,000 to $4,000.
But in the midst of climate change, why aren’t more builders and homeowners adopting the passive house standard?
Cost savings alone would be reason enough. Every dollar spent on insulation can likely reduce the cost of a heating system by a dollar, “a direct trade-off,” Orr said.
And for every one dollar spent sealing a house, the heating cost can be reduced perhaps ten-fold.
Quintupling the price of natural gas may finally get people serious enough about energy-efficiency, Orr suggested with a chuckle.
“Either that or some legislative body is going to say you’re going to do it,” he added.
“It also bothers me a great deal to see the misconception that people have about energy in buildings.”
For example, homeowners adding an inch and a half of Styrofoam when they install new siding.
“I defy them to find (the payback) on their energy bill after they’ve done it,” Orr said.
Unless people tackle the two biggest heat losses—air leakage and the basement—“you’re barking up the wrong tree.”
It’s a concern Marvin shares.
But Orr “just keeps on plodding along . . . and just kind of laughs when I tell him how frustrated I am,” Marvin said.
In Saskatoon, Orr has done a “chainsaw retrofit” of a house, wrapping it in polyethylene to make it airtight, adding R42 insulation from top to bottom, and replacing windows and doors.
He is now advising on a project Marvin leads, the proposed Buffalo Ranch zero-carbon community near Wanuskewin Heritage Park.
“He’s such a soft-spoken, rational and pragmatic person,” Marvin said of Orr. “You’ve got to love the guy.”